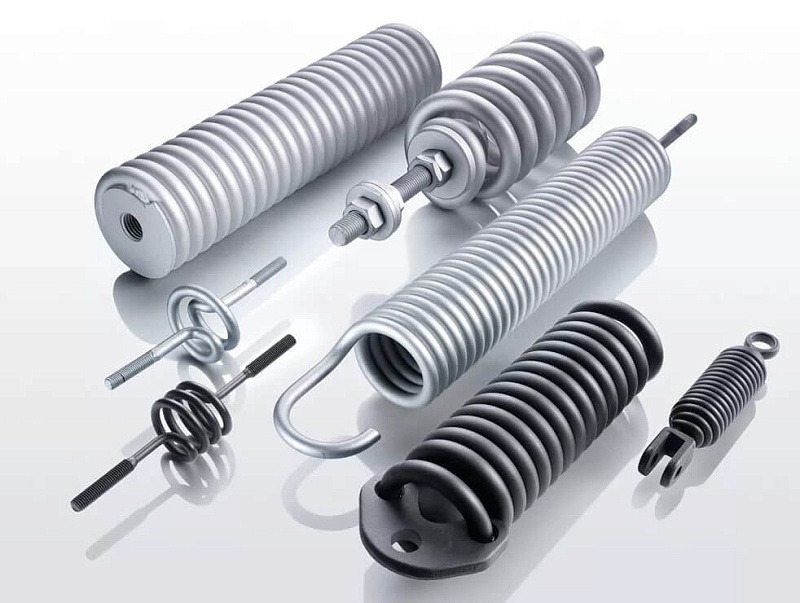
Общие сведения
Металл в изделии тем лучше сохраняет форму при деформации, чем выше его предел текучести. Чем ниже предел текучести материала, тем хуже прочностные характеристики металла и, соответственно, тем меньшие нагрузки способно выдержать изделие, тем быстрее достигается предел прочности — максимальное механическое напряжение, которое материал выдерживает без необратимой деформации (разрушения).
И наоборот: чем выше предел текучести, тем лучше материал сохраняет форму при механических воздействиях, тем выше его прочность. Это свойство особенно важно для сплавов, из которых изготавливаются пружинные стали.
Характеристики, физические свойства пружинных сталей
Характеристики материала определяют область его применения. Главным физическим свойством, которое выделяет пружинную сталь среди других сплавов железа с углеродом, является большой предел текучести. Поэтому изделия из нее способны возвращаться к исходной форме после деформирующих воздействий.
Необходимое свойство пружинных сталей — высокая прочность. Под воздействием на сжатие или ударных воздействиях кристаллическая структура сохраняет свою целостность.
Важным качеством является также коррозионная стойкость. Различные легирующие компоненты (особенно, хром), окисляясь под воздействием кислорода воздуха формируют защитную пленку, которая препятствует взаимодействию железа с окисляющими веществами и возникновению кислотно-восстановительных реакций, обеспечивает сопротивление к химической коррозии.
Виды пружинной стали, факторы влияющие на выбор
В России пружинная сталь обычно производится из низколегированных сплавов с общим содержанием добавок до 2,5%. Большинство американских и европейских стандартов указывают на использование среднеуглеродистых и высокоуглеродистых хромосодержащих сплавов.
Однако, для улучшения эксплуатационных качеств в большинство рессорно-пружинных сплавов включают кремний. Чтобы получить сплав с заданными свойствами используютcя добавки марганца, никеля, вольфрама, меди, ванадия, кремния, азотистых соединений. Это также определяет многообразие марок сплавов. Таким образом, можно выделить два вида пружинной стали: низкоуглеродную сталь и легированные сплавы.
Характеристики этого материала: сочетание прочности и упругости, гибкости и сопротивляемости к появлению изломов и трещин, коррозионная стойкость. Поэтому, из рессорно-пружинных сплавов изготавливаются металлоизделия, эксплуатационные свойства которых подразумевают способность материала сопротивляться упругой деформации, т. е. многократно восстанавливать исходную форму после деформационных изменений на изгиб и скручивание. К таким изделиям относятся все виды пружин, торсионов и рессор.
Маркировка рессорно-пружинной стали
Маркировка наиболее широко применяемых сплавов описывается в ГОСТ 14959-79 и ГОСТ 13764-86. Маркировка начинается двумя цифрами, которые обозначают количество углерода. Затем буквами указываются вещества, использованные для легирования, а цифрами — содержание добавок в округлении до целого значения. Если цифры нет, то легирующих элементов менее 1%.
В стандартах описаны:
- углеродистые стали, маркированные только цифрами (например, «сталь марки 65»);
- легированные сплавы марок 50ХГ, 50ХГФА, 55С2, 51ХФА, 60С2, 60Г, 60С265Г, 51ХФА, 60С2, 60С2А, 60С2ХФА, 65Г, 65С2ВА, 70С3А.
Расшифровка буквенных обозначений элементов:
- Г — марганец;
- С — кремний;
- Х — хром;
- Ф — ванадий;
- В — вольфрам;
- Н — никель;
- А — азот.
Примеры расшифровки:
- сплав 50ХГ с содержанием 0,50% углерода и менее 1% хрома и марганца;
- в составе сплава 65С2ВА соответственно 0,65% углерода, 2% кремния и менее 1% вольфрама и азота.
Самыми распространенными в России марками пружинной стали можно считать 60Г, 65Г и некоторые другие из перечисленных выше. Содержание углерода в них находится в диапазоне от 0,5 до 0,7%. Применяется также сталь с содержанием углерода от 0,7 до 0,9% (т. н. «инструментальная сталь»).
В Америке наиболее часто используют марку ASTM A228, которая часто обозначается как «музыкальная проволока» (Music Wire), содержание углерода в которой доходит до 0,95%.
Марки и область применения пружинной стали
Большинство марок предназначены для изделий, подвергающихся специфическим нагрузкам. Несколько примеров:
- из сплава 50ХГ изготавливают рессоры и пружины для автомобильного и железнодорожного транспорта;
- пружинную сталь 50ХСА используют для изготовления пружинок для часов;
- из стали 60Г можно производить любые детали пружинного типа с высокими требованиями по износостойкости и упругости;
- комплекс свойств сплава 50ХФА позволяют использовать его для изготовления измерительных лент, а также деталей, от которых требуется прочность и сохранение формы при повышенном нагреве.
Сталь практически всех указанных марок можно использовать для изготовления важных конструктивных элементов, к которым предъявляются высокие требования по усталостной прочности.
Технология производства пружинной стали
В производстве пружинных сплавов особое внимание уделяется измельчению зерна. Такая корректировка внутренней структуры металла повышает его сопротивляемость мелким пластическим деформациям, упругость и, в конечном итоге, релаксационную стойкость готовых изделий (пружин).
В отличие от сплавов, которые приобретают свои специфические свойства только благодаря включению в их состав особых легирующих компонентов, для пружинных сталей особое значение имеет метод обработки после выплавки, особенно режим «закалка — отпуск».
Термическая обработка, закалка и финальный отпуск
Обычной технологией является закалка (закаливание) низколегированной стали, в процессе которой металл нагревается выше определенной критической точки. Для пружинной стали рекомендуется выполнять закаливание в диапазоне температур от +800С до +950С. Использование этой технологии позволяет повысить предел текучести. Вследствие этого улучшаются характеристики стали по сопротивляемости деформирующим воздействиям.
Однако, результатом этого процесса является также формирование в материале мартенсита — углеродного образования, появляющегося в закаленном сплаве и выраженного пластинчатой (игольчатой) микроструктурой. Этот раствор углерода повышает ломкость металла, резко уменьшает его упругость. Для разрушения мартенситных соединений применяется отпуск при средних температурах (примерно, +4000С или немного выше).
Усовершенствованной технологией является отпуск в соединении с повторной термической обработкой - нормализационным отжигом (нормализацией металла).
Процесс нормализации заключается в нагреве до высокой температуры, выдержке в течение короткого времени и последующем охлаждении. Во время, которое требуется металлу для охлаждения до температуры окружающей среды, из него уходят лишние напряжения. В принципе, нормализация в определенной степени происходит в процессе естественного остывания металла. Это требует дополнительного времени и не дает идеального результата, но допускается для менее ответственных изделий.
Трудности работы с пружинной сталью
Ухудшение свариваемости
Необходимость применения технологии закаливания нарушает микрокристаллическую структуру, создавая прочный, но неоднородный внешний слой металла. В процессе сварки происходит локальное расплавление закаленного слоя. Выполнение сварки без учета особенностей, которые металл приобретает после закалки, может привести к формированию неоднородного слабого шва. Также возможно трещинообразование в зоне шва.
Трудности с резкой материала
Пружинные сплавы очень прочны. Соответственно, и требуются значительные усилия, чтобы разрезать деталь.
Заключение
Требования к эксплуатационным качествам пружин обусловливают особенности производства пружинной стали. Особую важность в этом процессе играет термическая обработка металла. Полученный материал, благодаря своим прочностным характеристикам и упругости, находит широкое применение в промышленности.